Sustainable Construction: Building a Better Future
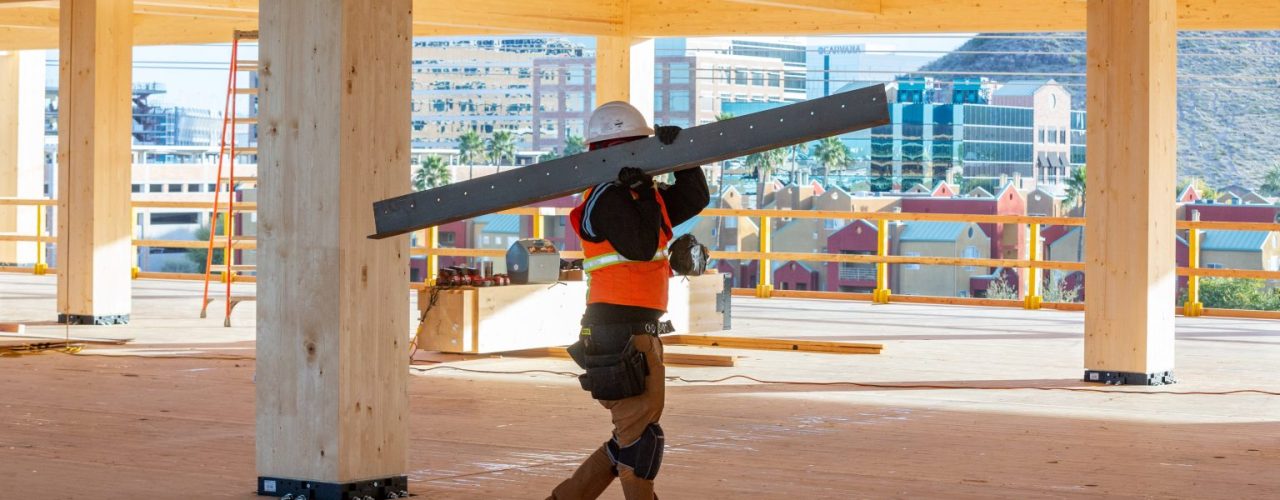
RSP’s Mike Duffy, along with the assistance of Mortenson’s Chase Gibbs, sheds light on the latest advancements in sustainable construction, highlighting The Beam on Farmer as an exemplary model for scalable sustainable development.
Architects and designers like to imagine that we’re saving the world one project at a time. But with the building industry responsible for 40% of carbon emissions, most of the built environment is part of the problem and not the solution. So we must challenge ourselves, how can we make an impact and reduce the carbon footprint of the buildings we design and build? The good news is that materials, technologies and new ideas are continuing to change the landscape.
Pushing the limits, in our own communities and across the industry, we are getting ever closer to minimizing the complicated issue of carbon emissions. We already have ways to use passive and renewable energies to heat, cool and light a building. While many sustainable features are consistently integrated into new buildings today, some of these practices have not yet become a standard. Sustainability can be oversimplified, when it comes time to finalize the design, and, at times, it is seen as purely an upfront cost, rather than looking at the bigger picture. As new materials, design strategies and technologies bring down costs, and we have the collective will to reduce carbon emissions, we are looking at a future where every building is environmentally neutral at a minimum, and ideally, environmentally restorative.
Furthermore, when the design takes an integrated and holistic approach to sustainability – with the design team, builder, and owner all at the table – we have found that is where the magic happens. Together, we are able to make collective, informed decisions while remaining focused on the bigger picture to reduce the carbon footprint and achieve our clients’ goals. This collaborative approach integrates sustainability into the design, rather than solving for it in a disjointed way.
A Real-World Case Study: The Beam on Farmer
The Beam on Farmer, a new project in Tempe, Arizona, is the cornerstone to the path to a more sustainable future. The Beam is the first mass timber office building in Arizona and sits at 184,000 SF and five-stories. In Arizona, where we are simultaneously experiencing record-high temperatures along with a development and population boom, planning for a more sustainable future is not optional.
Our client, Mortenson, is the developer, the general contractor, and will be soon calling The Beam on Farmer home upon opening, taking over the ground-floor space for their Arizona team. They had a bold vision for the project and for limiting its impact on the environment, while attracting the next generation of talent. To their immense credit, they came to us with a commitment to using mass timber construction from the very beginning. This vision came with design challenges to be sure, but the materials and strategies we used offer a way forward for the design industry without slowing down development.
Chase Gibbs, project executive at Mortenson said it best: “We know the market is booming in Tempe and we wanted to take advantage of the location, adjacent to Arizona State University and the expectations of future workforce. The market is so competitive, and we believe The Beam on Farmer, offering a unique experience with CLT, will be a differentiator for recruiting and a transformational, healthy workplace experience.”
Mass Timber: The Sustainable Construction Material of Choice*
To define our terms, mass timber refers to all mass-produced timber products manufactured by gluing thin wood boards together. The category includes glue-laminated timber (glulam) and nail-laminated timber. More specifically, cross-laminated timber, or CLT, is made by gluing layers of wood perpendicular to each other. This gives it a more rigid structure that does not shrink. The Beam on Farmer utilizes both mass timber products and CLT and we are using the terms somewhat interchangeably here.
Architects have used mass timber and CLT for decades in Europe. But these materials have been slow to make their way into projects in the U.S. because of code restrictions and a smaller supply chain. Thankfully, that is changing because CLT buildings can sequester as much carbon as a traditional concrete building creates. That means every CLT building is not just minimizing its own impact on the environment, but it has the potential to essentially cancel out the environmental impact of an existing concrete building.
The building is under construction and, from our client’s perspective, Chase adds that “Every person that steps foot in the building, even in its current state, is blown away by the unique feel the mass timber brings to the space. This building is redefining what it means to work in the office.”
Sustainable Construction by the Details
People who aren’t familiar with mass timber often look at wood products and imagine deforestation on a large scale. But responsible mass timber/CLT manufacturers use sustainably-sourced materials and renewable resources, with a carbon footprint that is typically 30-40% smaller than a traditional concrete building. When the tree is alive, it sequesters carbon through the photosynthesis process. The lighter structure of the material also helps to reduce carbon impacts.
In the spirit of full disclosure, not all mass timber structures are sustainable—the question of biogenic carbon, life span of the building (i.e., how long the carbon will be sequestered), how quickly replacement trees are planted, and the end-of-life cycle are all variables in how “green” the product is. What is clear, however, is that mass timber construction has powerful potential to be a highly sustainable weapon in the battle against climate change.
Despite the clear sustainable benefits of laminated timber construction, North America has lagged behind Europe in the production of mass timber and development of mass timber projects. As architects, we are seeing more questions about the process and an uptick in demand, and we see the material becoming far more popular in the near term.
As Chase explains, “The wood, once installed at The Beam on Farmer, will sequester almost 2,600 metric tons of CO2. This building is not only paving the way for setting new standards for the sustainability in the built environment in our own community, but it offers an innovative approach to the actual construction process. We were able to go from the ground up in only 4 months with half the work force it would take on a typical structure of this size. This is a critical accomplishment in the market we are in today.”
A New Process for Sustainable Construction
As architects, developers, owners and contractors learn more about mass timber and how to best build with it, the more efficient the process will become. For every mass timber project, it’s important to have the supplier at the table early on because it is inherent to the design process. The structure is entirely prefabricated offsite, which means that every connection and every penetration has to be designed and coordinated up front and accurately modeled in 3D. Each manufacturer has unique ways in which they approach the fabrication process, so it is crucial to have them involved early in the design process.
During design for The Beam, we really studied the grid spacing, beam depths, and how to create the most economical and flexible floorplate. In the past, one of the drawbacks to mass timber construction was that it required a denser column grid than concrete or steel to minimize structural depths. The added height gave us the opportunity to incorporate deeper beams. That also means the column grid is almost as sparse as a typical office building and gives the space an open, airy quality that matches the warmth of the wood and showcases the beautiful pattern created by the ceiling beams.
Built-In Wellness
Clients and building owners going for LEED or WELL standards will find that using mass timber may make the process easier. If you walk into a CLT building, it’s not hard to see why—we’re taking commercial office buildings that used to be a sea of cubicles and turning them into open, airy spaces full of natural materials and natural light. The material also has an inherent fire rating, which is why the slabs and beams can be exposed.
Reflecting on the process and ultimate outcome, Chase shares, “Working with RSP, early in the process, we were able to weigh our options and understand the impact of each, to make the best decision for the design and flow of The Beam on Farmer.” He adds, “Its location is optimal for walking to local amenities, and we have incorporated features throughout the facility to promote personal wellness, and a healthy building experience including a lobby that will have more of a hospitality feel to promote social interactions, a coffee bar, indoor outdoor collaboration space and a fitness room. Finally, and perhaps most unique, will be the touchless experience from ‘car to cube.’”
Again, as more CLT projects are built, the more designers and contractors will learn what other innovations can be added to the process. At The Beam, we designed a low-pressure underfloor air distribution system that is among the first in CLT construction. At only eight inches high, down from 24 inches in a traditional raised floor system, the low-pressure technology drives air to the perimeter of the building more efficiently. This increases thermal comfort, uses less energy and makes the system more flexible for users. Aesthetically, this allows for higher clear ceiling heights by eliminating the need for overhead mechanical systems and leaves more of the Mass Timber structure exposed and unobstructed.
Overcoming Challenges of Sustainable Construction
Early adopters of any new technology or material will face a learning curve and the task of explaining the benefits to others, and mass timber construction is no exception. Because the structure of The Beam is beautiful and the beams are deep, we pushed for an underfloor air distribution system to eliminate overhead duct work. The industry standard in spec office is that deepest structure + ductwork = maximum clear ceiling height. If you can eliminate overhead mechanical and maximize areas in which ceilings are open to structure, the clear height to your deepest beam is no longer as critical.
Perhaps a more notable challenge is that building codes across the country have simply not caught up with this type if construction yet. But things are changing. In the past, project teams may have had to get engineering judgments and commission independent testing to use CLT outside of the code, but the 2021 IBC adds new provisions that allow for taller mass timber structures. That, of course, means a more streamlined process for a material that could very significantly reduce carbon emissions across the country and around the globe.
The Beam may be the first CLT project in Tempe, but the city anticipates that it won’t be the last. Mortenson is already scheduled to move in as the ground-floor tenant and other tech-focused companies are expected to lease the upper floors as Tempe grows into its reputation as an innovation hub.
*Read some of the latest research on the use of CLT here.
About Guest Author Chase Gibbs
Chase Gibbs has been an integral leader in the development and construction of The Beam on Farmer. As project executive, he is passionate about building one-of-a-kind experiences that shape our communities throughout Arizona. With the drive and ability to solve complex challenges with think creatively, Chase has led some of the firms most unique landmark projects throughout the state including American Family Fields of Phoenix for the Milwaukee Brewers, Northern Arizona University’s Health and Learning, among others. Read more about Chase.